A Guide to Flexible Packaging
Need help deciding how to package your product?
The possibilities are endless – from rigid packaging to flow-wrap packaging to form-fill-and-seal packaging. But how do you choose? It all comes down to what your product requires and your own specifications.
Flexible packaging has taken the industry by storm, gaining popularity in both retail and big box stores. In fact, it’s the second largest packaging segment in the United States, according to the Flexible Packaging Association. Food packaging alone makes up 60% of flexible packaging shipments, followed by retail non-food at 12%, industrial applications at 6%, consumer products at 10%, institutional non-food at 3%, and medical/pharmaceutical at 9%.
So why should you consider flexible packaging for your product? Let these facts about flexible packaging guide your decision-making process.
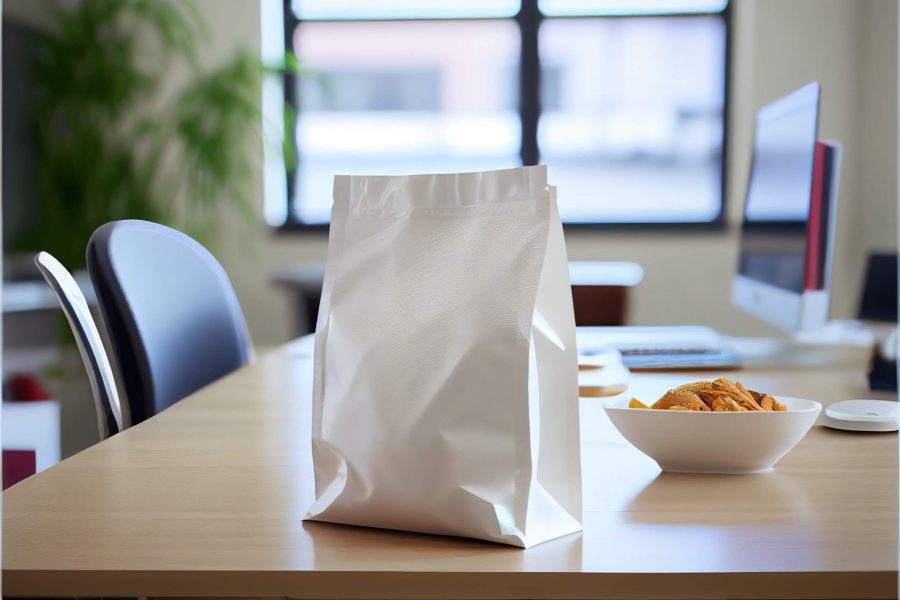
Comparing Flexible Packaging to Rigid Packaging
Flexible packaging offers a significant advantage compared to rigid packaging: it uses only a fraction of the plastic. In fact, flexible packaging weighs 70% less and occupies just 5% of the space as rigid packaging.
This reduction in materials and the associated savings in manufacturing and shipping costs make flexible packaging a much more affordable option than its rigid counterparts.
Flexible Packaging uses
70%
less weight
and
95%
less space
compared to Rigid Packaging
The Advantages of Flexible Packaging
When it comes to packaging, it’s crucial to have a barrier in place to protect the product from UV rays, oxygen, and moisture. This not only ensures the product stays unaffected by external contaminants but also helps preserve its aroma and shelf life. Flexible packaging is an excellent choice as it ticks off all these requirements, thanks to the characteristics below.
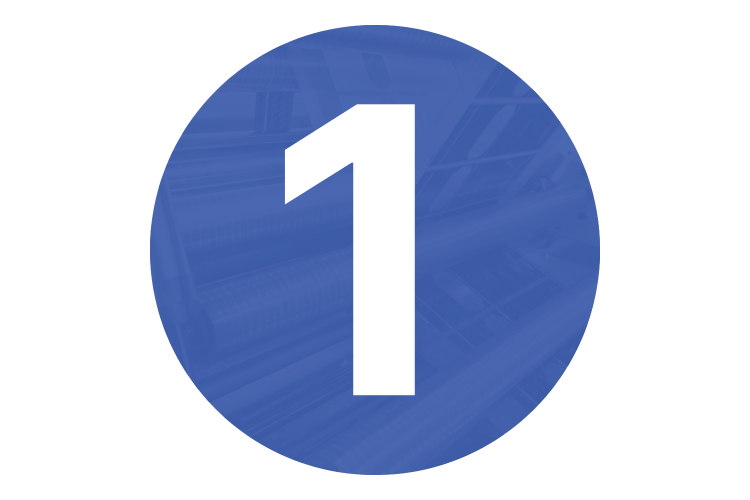
Materials Used
Flexible packaging is usually made from a film that has a low oxygen transfer rate.
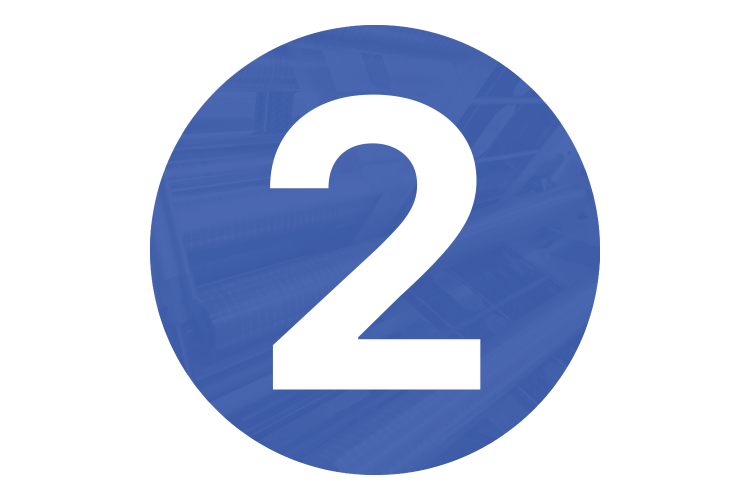
Product Construction
Flexible packaging is usually constructed using two or more plastic films laminated together.
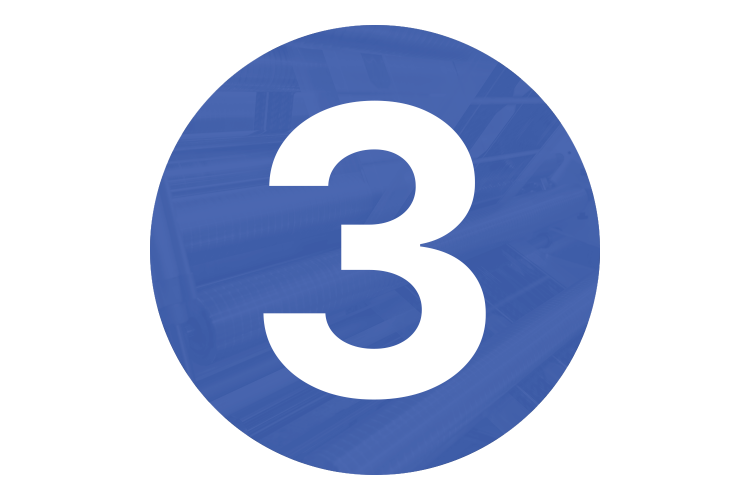
Printing Methods
Flexible packaging uses technology that avoids contact with the product it contains.
Flexible Packaging Materials
Keep your Products Fresh for Longer with Flexible Packaging
Flexible packaging utilizes a film with a low oxygen transfer rate (OTR), meaning it allows minimal oxygen to pass through. Metalized film, in particular, boasts an impressive OTR of zero. By purging the air with nitrogen before sealing, the shelf life of a package can be further prolonged.
Additionally, film also has a Moisture Vapor Transfer Rate (MVTR), which operates similarly to OTR. LLDPE (Poly), despite having a higher OTR, has a lower MVTR and allows for hermetic seals, making it a suitable choice for flexible packaging.
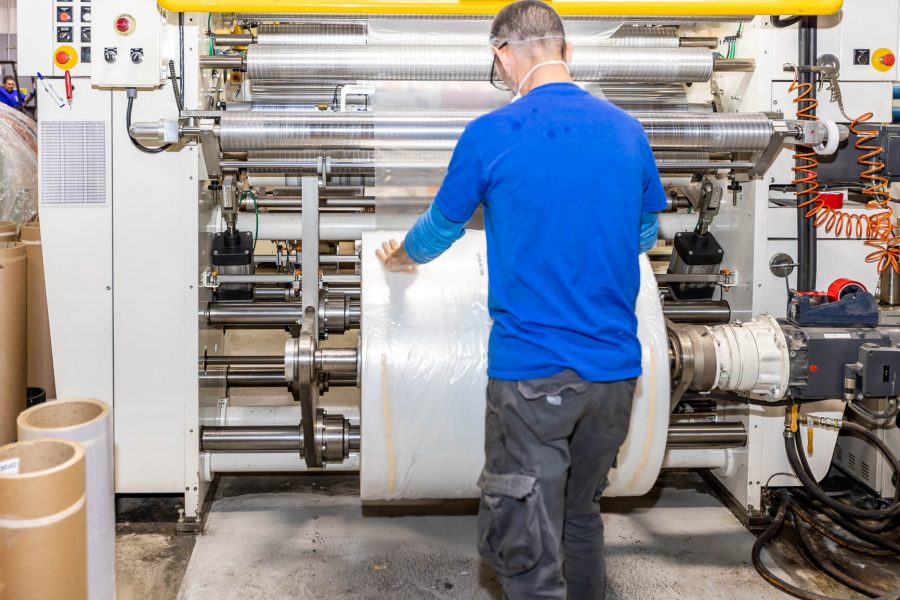
Flexible Packaging Construction
Reinforce Your Brand with Custom Flexible Packaging
Flexible packaging, commonly found in the form of stand-up pouches, is made up of multiple plastic films bonded together. These films, typically PET/Ink/LLDPE, provide various benefits.
PET, also known as Polyester or Mylar, forms the outer layer due to its strength and high melting point. The ink refers to the printing on the packaging, applied to the inside of the PET layer and covered by another film layer. LLDPE, or Poly, serves as the inside layer, offering moisture resistance and a low melting point. It is what creates the seal on the pouch.
Thickness is also an important consideration, with film usually ranging from 3-5 Mils (Thous).
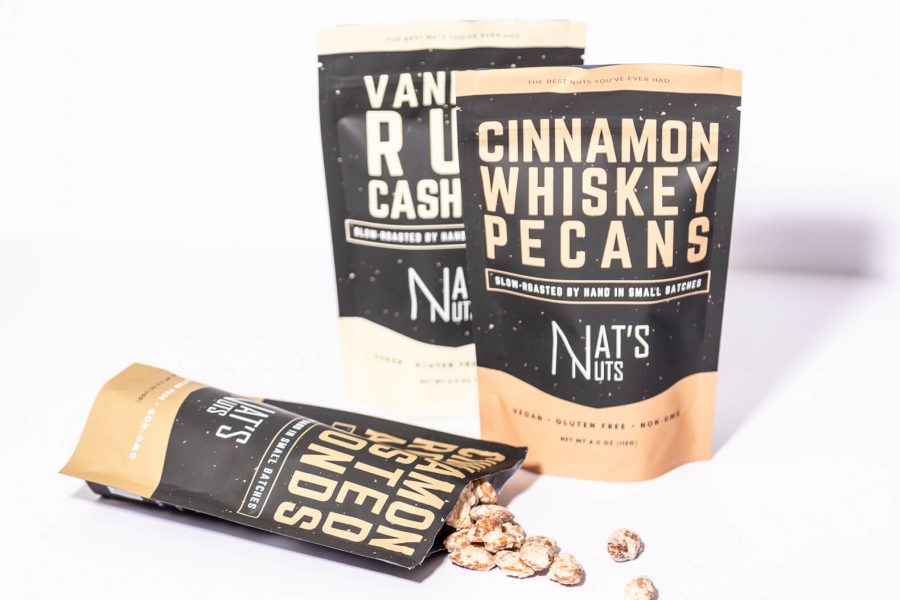
Flexible Packaging Printing
Protect Your Product From Ink Damage
To safeguard the product from ink during packaging, a printing technique called Reverse Trap Printing is employed. This involves printing a reverse image on the inner side of the outer film layer, creating a protective layer between two film layers.
However, this method may not be effective if the film used is not transparent. In such cases, the Surface Print process is used, where the printing is applied to the outside of the film.
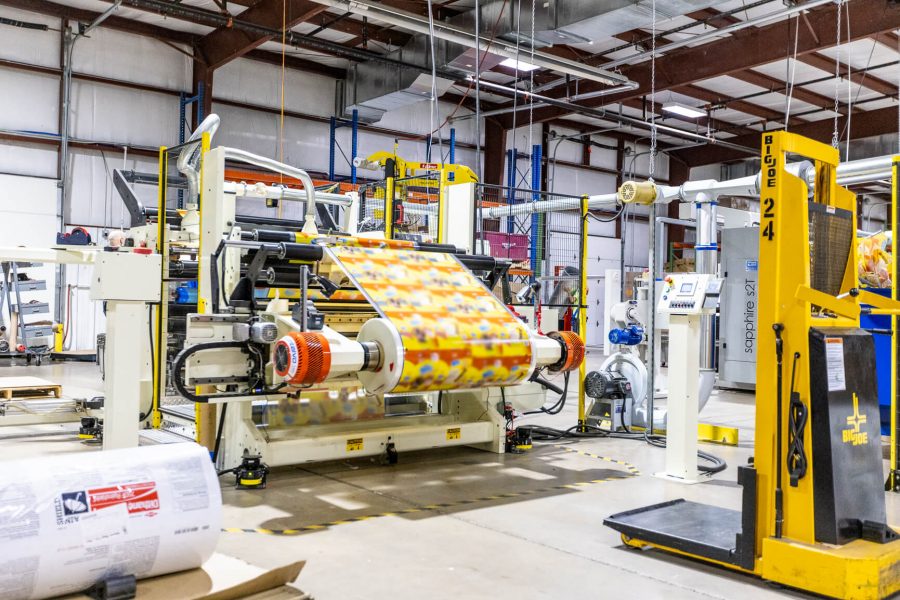